Miura’s industrial steam boilers are highly adaptive to the ever-changing steam demands of textile manufacturing facilities.
Whether for pre-processing, dyeing/printing, or the finishing of textile products, our steam boiler systems offer textile manufacturers a quick, reliable, comprehensive steam solution that is efficient, eco-friendly, and safe.
Competitive Advantages of Miura’s Complete Steam Solutions
Steam boiler technology has evolved over the years to provide textile producers with cutting-edge steam solutions. Textile manufacturers requiring high-quality and high-pressure steam can trust Miura’s advanced steam boiler systems to keep their facilities operating safely and at optimal efficiencies.
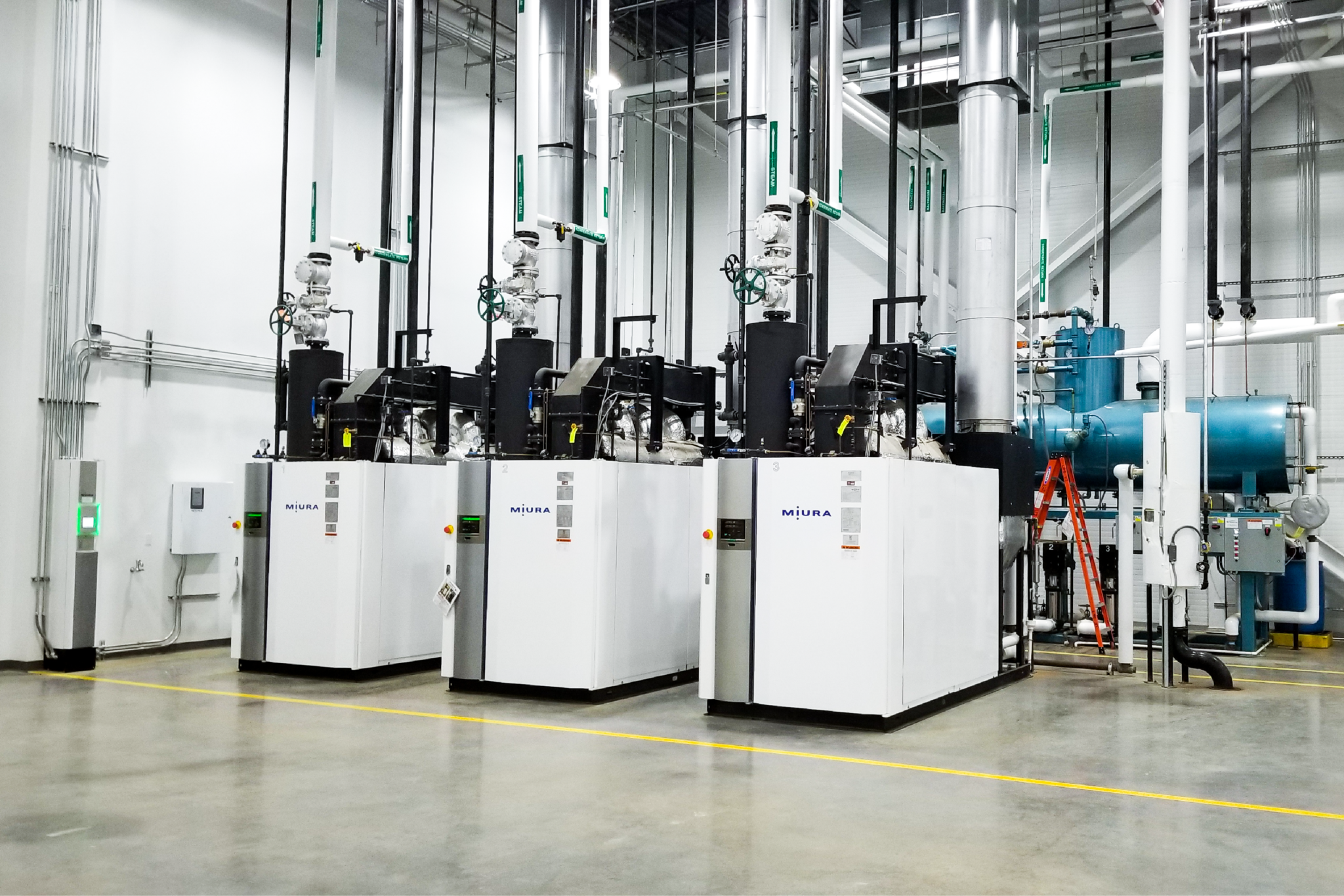
Efficient and Precise Steam Production
Textile production requires consistent, high-quality steam at precise temperatures for dyeing, pressing, and heat-setting processes. Miura’s low-water-content, vertical watertube design delivers rapid heat transfer and on-demand steam within five minutes from a cold startup.
- Instant steam availability eliminates preheating delays
- Only produces the steam needed—reducing fuel waste
- Precise temperature control improves dye consistency
Instead of running continuously, Miura boilers turn on and off automatically based on real-time demand, reducing fuel consumption and operational costs while maximizing fuel-to-steam efficiency. These rapid and automated startups and shutdowns mean our boilers produce only the exact steam needed, reducing fuel and energy wastage, lowering operation costs, and increasing fuel-to-steam efficiencies.
Reliable Performance & Smart Monitoring
Steam interruptions can ruin fabric batches, cause production delays, and increase costs. Miura’s remote boiler monitoring technology oallows operators to track boiler performance, detecting potential issues before they disrupt operations.
Regular inspections covered by Miura’s proactive maintenance plans help prevent boiler breakdowns and ensure our client’s steam boilers stay in optimal condition. Miura’s modular boiler configuration also means that only one boiler module is needed in reserve (and not a full system backup) to replace a boiler that is taken offline for routine maintenance or repairs.
- Automated alerts for proactive maintenance
- Modular configuration ensures backup steam is always available
- Routine inspections and maintenance plans prevent downtime
Miura’s modular boiler system means textile plants only need one reserve boiler instead of an entire backup system, making it a cost-effective, space-saving solution.
Safer By Design
Traditional firetube boilers store large volumes of water, increasing the risk of catastrophic pressure vessel failure. Miura’s low-water-content watertube design eliminates this risk while providing faster, safer steam production. Easy-to-read gauges, safety alarms, and zero confined space requirements for maintenance and inspection are just a few of the safety advantages of a Miura boiler system.
The low water content in a Miura boiler also means that water moves quickly through the tubes in a single pass before transforming into steam. Our boiler’s ultra-low water design and once-through operation help reduce the risk of catastrophic pressure vessel failure and an explosion.
- Minimal water content reduces explosion risks
- No confined space entry needed for maintenance or inspections
- Integrated safety alarms and easy-to-read gauges improve operator safety
Sustainability & Resource Efficiency
Textile production is water- and energy-intensive, making conservation a top priority. Miura’s once-through steam generation significantly reduces water usage while maximizing energy efficiency, all while helping manufacturers meet emissions regulations and sustainability goals.
- Lower water consumption per steam cycle reduces utility costs
- No wasted fuel on unnecessary boiler firing
- Compact, modular design saves valuable plant space
- LX-Series boilers: Low-NOx emissions (5ppm) for stricter compliance
- EX Dual Fuel boilers: NOx ratings as low as 30ppm
Our LX Gas-Fired steam boilers come standard at 20 ppm and can reach NOx regulations as low as 5 ppm nitrogen oxides (NOx) at 3% corrected O2. Depending on the model, our EX Dual Fuel boilers can achieve a NOx rating as low as 30 ppm. By reducing fuel waste and emissions, Miura helps textile manufacturers operate more sustainably while maintaining high-quality fabric production.
Power Your Textile Manufacturing with Miura
Steam is critical to textile production, and Miura delivers efficiency, reliability, and sustainability in one compact, cost-saving solution. Whether optimizing dyeing operations, improving energy efficiency, or ensuring uninterrupted steam, Miura is the only choice for textile manufacturers.
Contact Miura today for a full review and analysis of your boiler room setup. We will happily design a fully customized steam solution for your textile manufacturing facility.